The Future of Robotics and our IOSM Yard
Marketing
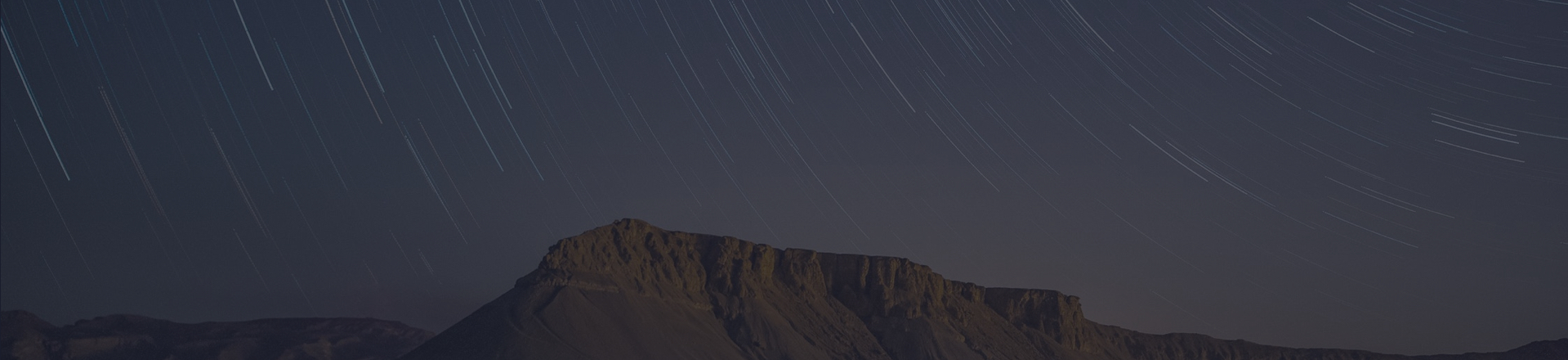
Part of our ambition for Prospero, our monthly newsletter, is to connect more directly with our community. In each edition, we will be sharing conversations, insights, and expertise from our Catapult team members, exploring how their roles affect us as an organisation, their impact on the wider sector and what drives them personally. This month, we sat down with Jeremy Hadall – Robotics Development Lead here at the Satellite Applications Catapult.
I come from a long line of engineers. My father was an electronics engineer, one grandfather was an engineering officer in the Navy and the other was a mechanical engineer. So it was always likely that I would follow in their footsteps. Not wanting to specialise in any particular area, I studied a BEng in manufacturing systems engineering at university as it felt like a more diverse field of study. My lecturers then encouraged me to stay on and complete a masters in engineering at Hertfordshire University. This postgraduate degree involved both general engineering and engineering management.
I gained experience in hydraulic robotics at university, but didn’t see it as a career when I left. That changed when I was asked to fix a broken robot system in my first job. From then on, I was hooked and soon moved to my first robotics job. I started as a graduate applications engineer at one of the biggest robot manufacturers in the world, ABB Ltd. Over eight years I worked my way through to more senior roles, ending up as a product manager.
Looking back, it was an incredible time to be working in the industrial robotics field. New features such as force sensors and lasers provided production line robotics with the ability to work with precision, unlocking many potential uses. Robotic development was also being driven by advancements in software, allowing us to simulate and network robots together in ways that had never been done before. Working alongside customers, I optimised production lines and carried out demonstrations and product support for ABB’s offline programming and simulation tool for robotic applications. I also led and managed project teams. Through end-to-end management of automation projects for customers, we produced novel concepts pioneering what people were doing with robotics.
The next significant career change saw me move to an international logistics company, Vanderlande. The internet was enabling a whole new platform of commerce for consumers. Machinery was now also capable of high-speed sorting and able to handle fragile items. A big accomplishment here was establishing the UK’s first home grocery delivery picking centre. The Dot Com Only Store (DCOS) allowed for increased efficiency in the fulfilment and traceability of home delivery orders, whilst also decreasing product damage. After the successful integration of the first DCOS, the client established three further sites within 24 months!
In 2010, I joined the Manufacturing Technology Centre (MTC) – part of the High Value Manufacturing Catapult. Over the next decade at MTC, we developed entire networks of robotics to work in unison through the growing use of digital tools. We applied multiple sensors to systems which enabled robotics to become more integrated into factory environments, pioneering new approaches to manufacturing challenges with robotics.
At MTC, I coordinated the strategy, roadmaps and growth of the automation group from the start of the company, securing the funding and delivery of five million pounds’ worth of state-of-the-art automation equipment in the first 18 months. But it wasn’t just about technology, the role was also about equipping businesses with the skills and knowledge they needed to benefit from automation. To achieve this, I led the delivery of seminars and training and was part of the team that created the company’s graduate development programme.
Although the evolution of robotic manufacturing has had a seismic impact on the manufacturing industry, the challenges addressed in the development of robotics had somewhat diminished. Looking for a new challenge is how I came to the Catapult. What we are trying to implement with robotic capability in the space sector is both quite challenging and experimental!
Over the years I’ve been involved in some really exciting projects, but one stands out from a collaborative point of view. This project at MTC involved developing new techniques and approaches for robotics with European companies. Working with experts from research centres in Denmark, Germany and Spain, we ran a programme providing consultancy for organisations, in particular SMEs. There was a huge range of projects and ideas we supported, everything from conveyor tracking solutions for automated production lines, autonomous delivery systems for Swiss Postal Service and product testing for start-up technology providers who have since grown into international players. One of those companies is now one of the largest robotic gripping technology suppliers in the industry. To have played a role in the initial industry testing really highlights what our collaboration achieved.
Other projects that really stood out were those around human and robot collaboration. These were very exciting and looked at how to get humans and robots working together safely and efficiently in a production environment. A great example of this is the work we conducted with a UK company called the Small Robot Company. Small Robot Company manufactures farming machinery utilising autonomous agricultural robotic capability coupled with artificial intelligence. Collaborating with the John Lewis Partnership, Google and leading academics, we developed a framework for how autonomous robots interact with humans. Rather than keeping humans safe by keeping them away from the robots, we flipped the problem around, looking at how the user would interact with the robot and what this meant for the safety functions on the robot. Focusing on what the user wants and how they will interact with the robot changes the way you think about robot functionality.
The KUKA robots we use are off-the-shelf robots that you would find in any automated car plant. As such, they’re optimised for typical manufacturing processes and not what we use them for! That means we have to develop a lot of customisation in the IOSM Yard. One of the reasons we chose KUKA robots is they are used by a lot of research centres in different fields of robotics. That means there is a community of people to engage with who might see similar problems, or who’ve tried various things with the robots already. This allows for thought sharing and collaboration on developmental aspects which the manufacturers never originally intended the robots to be capable of. In the IOSM Yard, we use the Robot Operating System (ROS). This is a robotics middleware suite providing software frameworks for robot software development; used by robotic researchers worldwide.
There are several features that make the IOSM Yard unique for testing IOSM satellite technologies. Firstly, as one of the largest facilities in Europe its size makes it unique and enables us to test large objects. Because of its size, we also have one of the largest motion capture systems in a UK space research facility. This system enables us to capture accurate data on the path and motion of in-orbit machinery attached to the robots during rendezvous scenarios. We can adapt the lighting in the facility so that we can replicate as closely as possible the lighting conditions in orbit. We are also developing a digital environment that enhances preliminary simulations. This will enable prototyping before we commit to utilising the IOSM facilities with customers. In situations where we may not be sure of the exact performance, this will provide better risk mitigation, creating a solution where physical testing is preceded by digital testing. To integrate the subsystems, ROS will eventually permit us to connect all these systems together. Right now, we have purposefully kept them separate to prove to individual subsystems before combining them into a complete system.
The facility has been open for about a year and we are still developing it (and probably always will!) to match customers’ mission scenarios. Working with companies aids the process, in that the facility will remain applicable to the novel in-orbit service technologies being developed. As far as future aspirations go, we would like to grow the size of the facility. Ultimately, this could lead to us being able to put larger objects in there and have more robots working together at the same time. This could be quite a challenge, but would set us aside as leading pioneers in the space sector.
It aids in the physical simulation of what would happen in a mission scenario by providing operators with a nice remote environment away from the IOSM Yard. We have rows of desks, a bank of screens and sofas, all of which help to provide a comfortable informal environment. The IOSM Control Room mimics how missions would work in reality, as it is separate from the test environment. As operators are not in the same room, you have to utilise the data coming directly from the IOSM Yard. The IOSM Control Room therefore provides a simulation of how we would operate systems in space. Companies can then also develop further training in how to operate systems in a remote environment.
I have been developing new capabilities for robotics all of my career and yet we’re still not using them to their full potential, so for me it’s still really interesting to see new ideas develop and grow. For me personally, developing ways to allow fully autonomous robots to work alongside humans in the space environment is particularly interesting. This partnership between human and robot work in space inherently presents added complexity. Despite the added challenges, it is exciting to think the technology developed will conduct missions at very remote distances from Earth.
Looking at in-orbit servicing we know what is possible mechanically, but the control system behind the mechanics is where we really are going to see change. That means the development of autonomous robots that are able to carry out more tasks on their own without human intervention. However, this means training the robots to deal with any eventuality, which is not going to be easy. For example, we don’t necessarily know what condition a satellite will be in when the robot arrives to service it. It might be functioning perfectly, but it could have been damaged during deployment or by orbital debris during its lifetime in space. Equipment like antennas, solar panels or even thermal shielding might not be where they should be and the robot will have to detect this and deal with it without human intervention. That level of autonomy is someway off, but it is where we should be heading.
One of the biggest interaction challenges for any autonomous robot is understanding human intent and reacting in a way that the human can understand and can trust the intent of the robot. Essentially will the robot do what it should do, and will this remain within the guidelines of what is logical and safe? There are some really interesting examples of how this is not working terrestrially, where people deliberately try to fool the autonomous robot into making a mistake. In these scenarios the robots generally stop and default to a ‘safe mode’ simply because they have not been trained to understand what the human intends to do.
There are lots of small start-ups and at the moment it’s difficult to say which of these start-ups are going to be really successful. This is because until they get some ‘flight heritage’ by demonstrating their technology in-orbit, investment is hard to come by. This is a big challenge for the smaller companies, it might be that they are bought out by a larger organisation who can fund the development of flight hardware. Those larger companies (Airbus, Northrup-Grumman, GMV, Lockheed-Martin, etc…) are already quite advanced with robotics programs, however they might not have all the technologies needed for commercial success.
We have actually worked alongside Airbus and some of its Advanced Concepts and Robotics Team. This work involved Airbus’s Versatile In Space and Planetary arm (VISPA). The VISPA robotic arm is capable of high-fidelity, accurate and complex operations. VISPA was tested within the IOSM yard simulating varied scenarios all of which involved a chaser and a target. Utilising the track-mounted servo-driven KUKA robot, we emulated proximity awareness and approach guidance with the manipulator on inspection, repair and maintenance scenarios.
I would like to know why we don’t treat the space environment in a more sustainable way. Humanity has tended to do things that suit it and worry about the consequences later. We’ve polluted the oceans, cut down forests and are now having to deal with the consequences. We’re now starting to repeat the same mistakes we’ve made on earth with our orbital environment.
We’ve tended to think of space as being so big that space debris will never be a problem. However, we are heading toward a point where space becomes cluttered, and the Kessler syndrome could become a real phenomenon. Kessler describes a phenomenon in which the density of objects in Low Earth Orbit (LEO) is large enough that collisions between objects could cause a cascade effect. Each collision could in turn generate space debris that exponentially increases the likeliness of further collisions. If this were to happen, the implications could significantly hinder space activities and the use of satellites in specific orbital ranges for future generations.
So, space sustainability needs to become more important. Removing dead satellites and debris, servicing satellites that have failed and have the potential to become debris needs to become the norm. All these processes will not only be commercially important, but if we have the intention to continue to be a spacefaring species, they will be crucial from a sustainable point of view. So, there is a bit of an urgency around it but perhaps not enough.
Fortunately, there are a lot of different agencies and organisations now considering this following research into this area of space environmentalism. Certain parameters now ensure if you intend to launch you have to be able to remove the spacecraft within a certain amount of time and have this built into the mission plan, but in many instances, there is no legal requirement or ways to check if it happens. Although launch criteria is getting stricter in some parts of the world, the danger is it might drive companies away from pursuing launches there as instead they will likely go to places where the launch criteria are not so strict.